From the invention of the modern automobile to today, concept cars have been a tantalizing glimpse into the future. From fuel-cell-powered vehicles and electric engines to self-driving cars, these prototype designs are often years ahead of their time.
But what is not always appreciated is that press brake technology has played an essential role in bringing these concepts from paper to reality. In this article, we explore how precision bending and forming equipment can help bring even the most daring visionaries\’ dreams to life.
A Brief History of Press Brakes
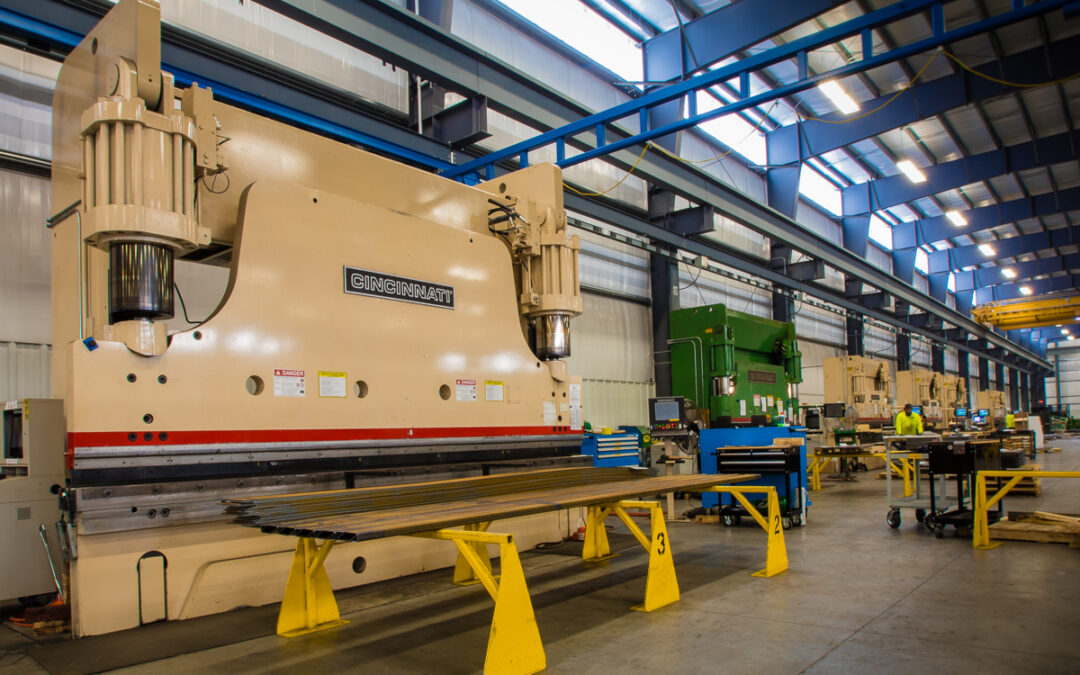
Source: owenmetalsgroup.com
The press brake has come a long way since its invention in the late 19th century. Initially, it was used to bend and form sheet metal into desired shapes for industrial purposes.
Over time, the technology has evolved and adapted to new applications such as prototype development. A Brief History of Press Brakes illustrates how this versatile machine went from an innovative concept to a widely used tool today.
In 1887, German engineer Ewald Fuchs developed the first power press brake which featured two pivoted arms connected by gears enabling vertical movement that bent sheet metal with great accuracy. This innovation made mass production possible and revolutionized manufacturing processes around the world.
By 1922, Otto Graf had further refined press brakes by introducing hydraulic pressure control systems allowing for greater precision when forming metals at high speeds – an essential factor in producing prototypes quickly and efficiently without compromising quality or safety standards. Throughout World War II, press brakes proved themselves invaluable for creating parts needed on tanks, planes, ships, and automobiles while also providing crucial support during Disarmament efforts following the conflict end; they were essential machines in making sure weapons destruction remained precise but expediently executed according to protocol agreements between Allied forces at the time. Today modern press brakes continue to be upgraded with advanced features that allow them to keep up with ever-changing demands of product design while still maintaining their superior level of efficiency when it comes to producing prototypes with maximum speed and accuracy; thus securing their place as one of the industry’s most indispensable tools when it comes to rapid prototyping development projects worldwide!
How Press Brakes are Used in Prototype Development
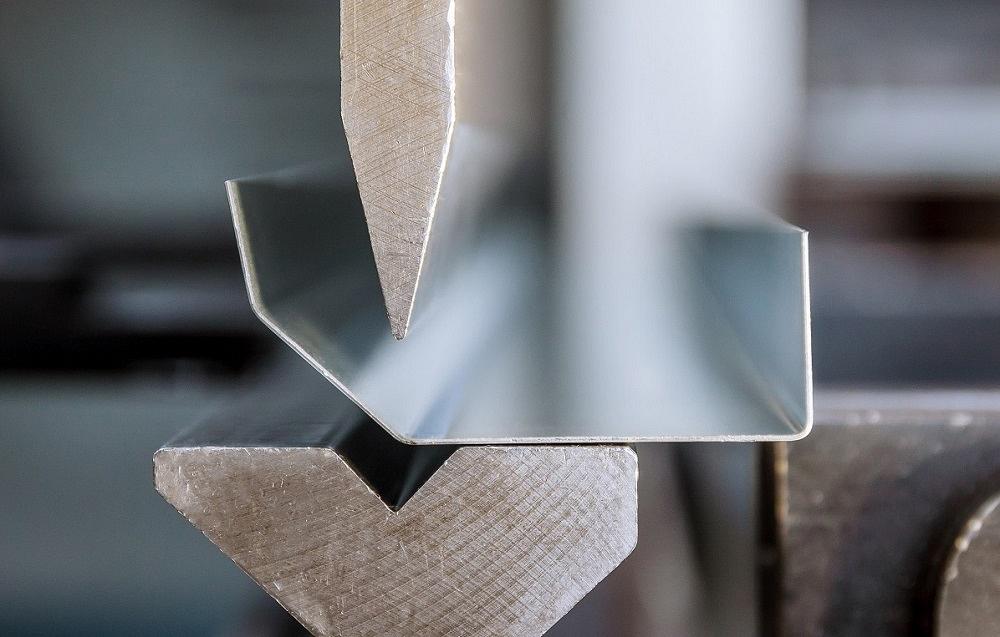
Source: www.thefabricator.com
Press brakes are an essential part of the prototype development process. They allow for precise and accurate bending of sheet metal, creating components that can be used in a variety of different types of vehicles – from concept cars to production automobiles.
With press breaks, designers can create parts with varying levels of complexity, allowing them to quickly iterate on designs and test out multiple ideas before settling on one final product. This flexibility makes press breaks invaluable when it comes to prototyping new design concepts.
The use of press brakes also reduces the cost and time associated with manufacturing prototypes due to their ability to form complex parts more efficiently than manual methods such as hand or hammer forming. Press brake machines can bend materials without sacrificing material strength or integrity, helping designers produce strong yet lightweight components that meet all safety requirements.
Additionally, they offer repeatable precision which allows engineers to consistently produce quality products without having to constantly adjust settings or measure each component manually. Overall, press brakes greatly enhance the speed and accuracy at which prototype development can take place by providing efficient fabrication solutions for a wide range of vehicle designs – from concept cars through production models – while still ensuring quality results every time.
Benefits and Challenges of Using Press Brakes for Prototypes
Source: www.thefabricator.com
Press brakes are a critical tool used in the development of prototypes. With their ability to bend metal components into shape, press brakes can help bring concept cars from the drawing board into reality.
There are numerous benefits and challenges associated with using press brake technology for prototype development. One major benefit is cost savings; since no dies or molds need to be created, costs for prototype production can be kept low.
Additionally, press brakes also allow users to make changes on the fly during fabrication without additional setup time as would be required with other methods such as stamping or injection molding. This makes it easier for prototypers to quickly refine designs and create more accurate representations of what will eventually become mass-produced products.
At the same time, certain challenges come along with using press brake technology for prototyping purposes. One issue is accuracy; because there are so many variables involved in bending sheet metal (such as material thickness, type of steel being bent, etc.
), even experienced operators may not consistently achieve perfect results every time they use a press brake machine. Another potential problem is speed; while automated machines may work faster than manual ones, both types require considerable setup times which eats away at overall productivity levels when compared to other methods like die casting or 3D printing processes which have much shorter lead times between design iterations due to their lack of complexity in terms of tools needed and process steps followed .
Overall though, the advantages offered by using press brakes far outweigh any drawbacks associated with them when it comes to developing high-quality prototypes that accurately represent future series production models—making them an essential part of modern automotive innovation!
Advantages of Using Automated Press Brake Systems
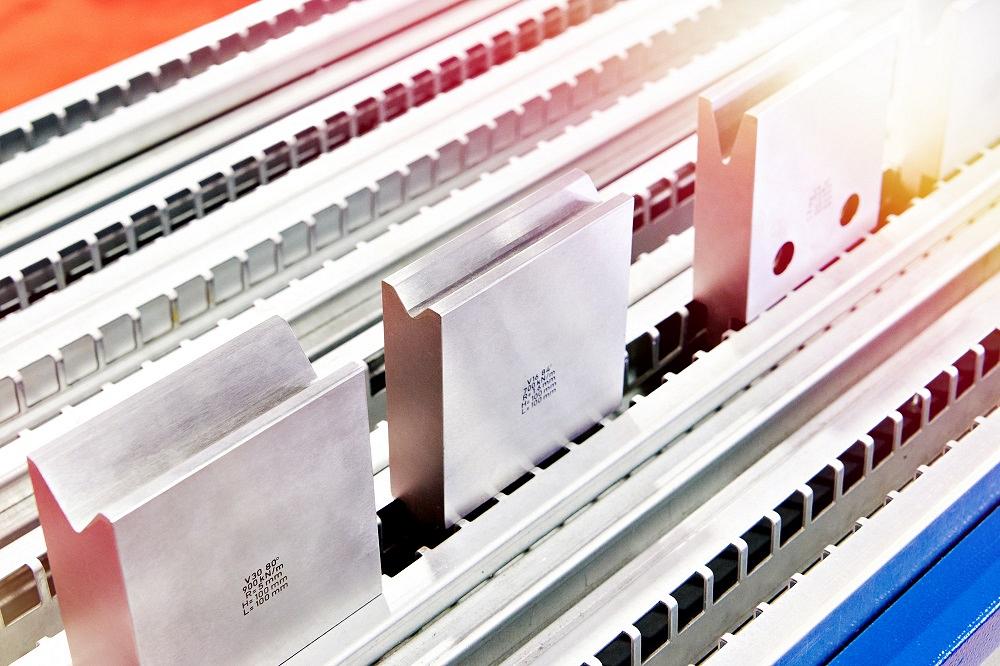
Source: www.thefabricator.com
Using automated press brake systems has several advantages when it comes to prototype development. Automated press brakes facilitate rapid prototyping, allowing companies to quickly produce prototypes and move on to the next stage of product development.
Automated press brakes also reduce waste and improve accuracy, as they can be programmed for precise measurements with no variation from one product to another. Additionally, the use of an automated system eliminates human error in production, resulting in higher-quality products and fewer defects.
Finally, these systems are cost-effective due to their ability to process multiple pieces quickly with minimal labor costs compared to a manual process. All of these factors make automated press brake systems ideal for developing accurate prototypes rapidly at low cost.
The Future of Prototype Development with the Help of a Press Brake
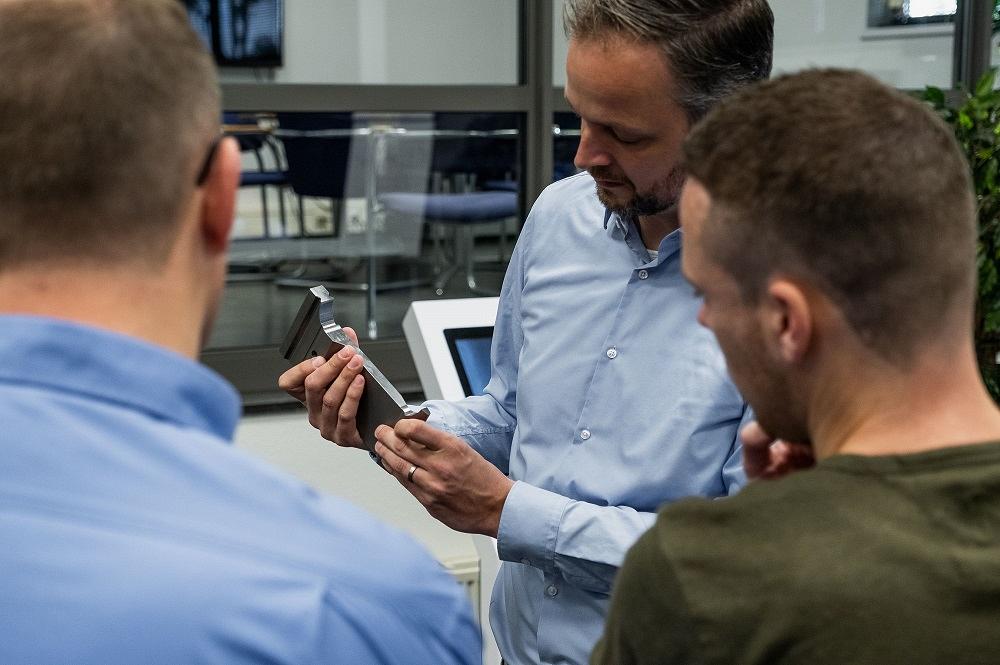
Source: www.thefabricator.com
The use of press brakes for prototype development has been on the rise in recent years. This evolution has helped to bring concept cars from the drawing board into reality quickly and efficiently.
The future of prototype development with the help of a press brake looks even brighter, as new technologies are being integrated to make this process more advanced than ever before. For example, advancements in laser cutting technology have allowed for increased precision when it comes to creating complex parts that may be necessary for prototyping certain vehicles or machines.
Automation tools such as robotics now allow manufacturers to produce multiple parts faster and without compromising quality control standards. Even 3D printing is making a significant impact on how prototypes are created using press brakes due to its ability to create intricate shapes quickly and cost-effectively. These developments mean that those who specialize in prototype development can now work at higher speeds while still ensuring accuracy and quality throughout their projects, resulting in shorter turnaround times between concept creation and completion of prototypes ready for testing against real-world conditions.
As a result, we will undoubtedly see further improvements in how prototypes are developed through the continued utilization of press brakes along with these modern innovations over time.
Conclusion
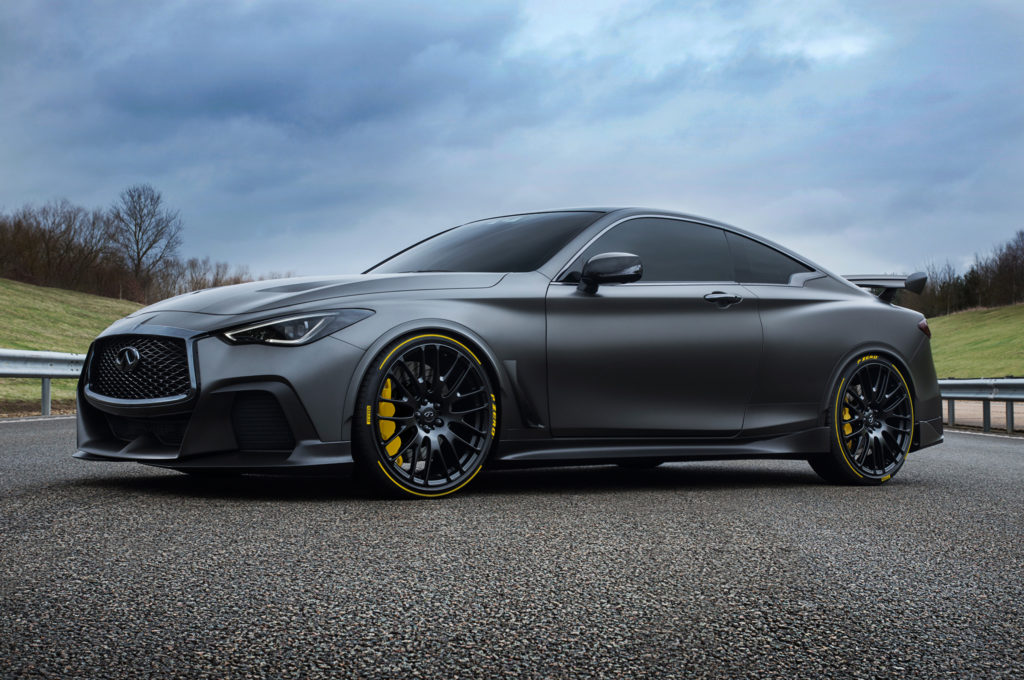
Source: www.pmw-magazine.com
The press brake machine has been a key factor in the development of prototype cars, allowing engineers to bring concept cars from their imagination into reality. This powerful and versatile tool provides fast and accurate bending processes for many different parts, making it an invaluable asset to any automotive prototype development project.
As technology continues to evolve, so too will the capabilities of this indispensable piece of equipment; ensuring that the future of prototype car design remains bright.